As medical packaging experts, we know the importance of providing you with packaging solutions that ensure your medical devices and products are safe and secure from the time it is manufactured, until the time it reaches your end customer, the patient. Our ISO certified cleanrooms have been recognized as some of the most advanced within the thermoform packaging industry, to ensure the highest quality standards are met. The approval process is key, which is why our industry leading prototype turnaround time (4.5 days) is key to getting samples to your team for review to expedite approval timelines. We work with you every step of the way from our award winning design, packaging validation, to your product being introduced to the medical market. Our team helps navigate these processes to make sure you achieve your medical packaging goals. We invite you to visit any of our medical packaging facilities to see our clean rooms and processes in place as we create simply better packaging.
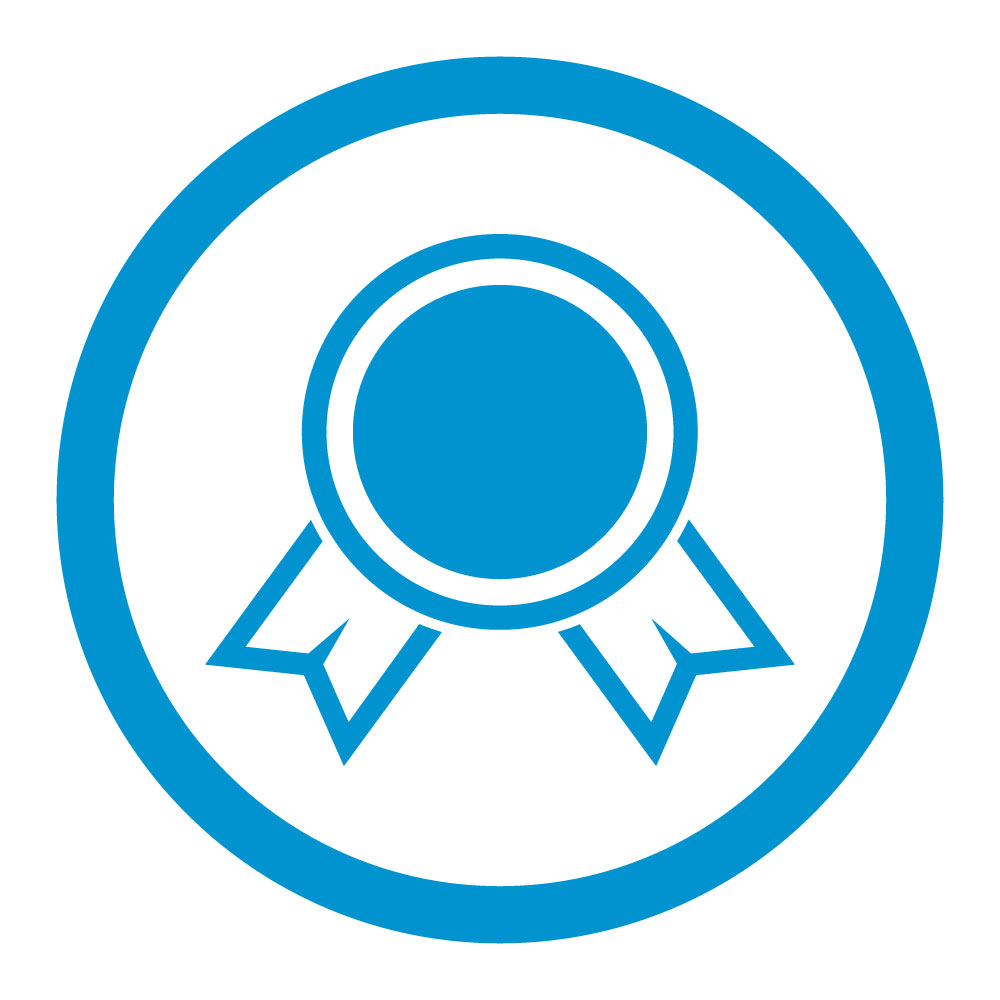
Award-winning
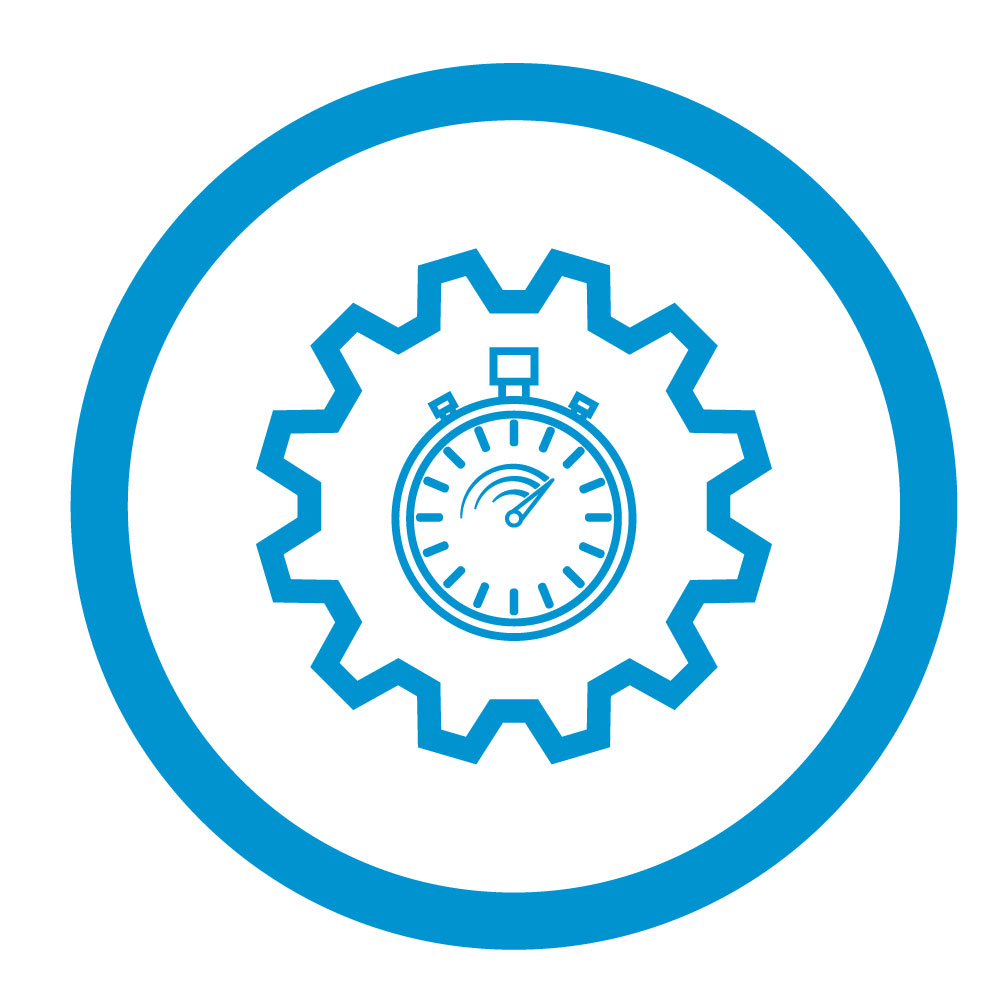
Rapid Prototyping
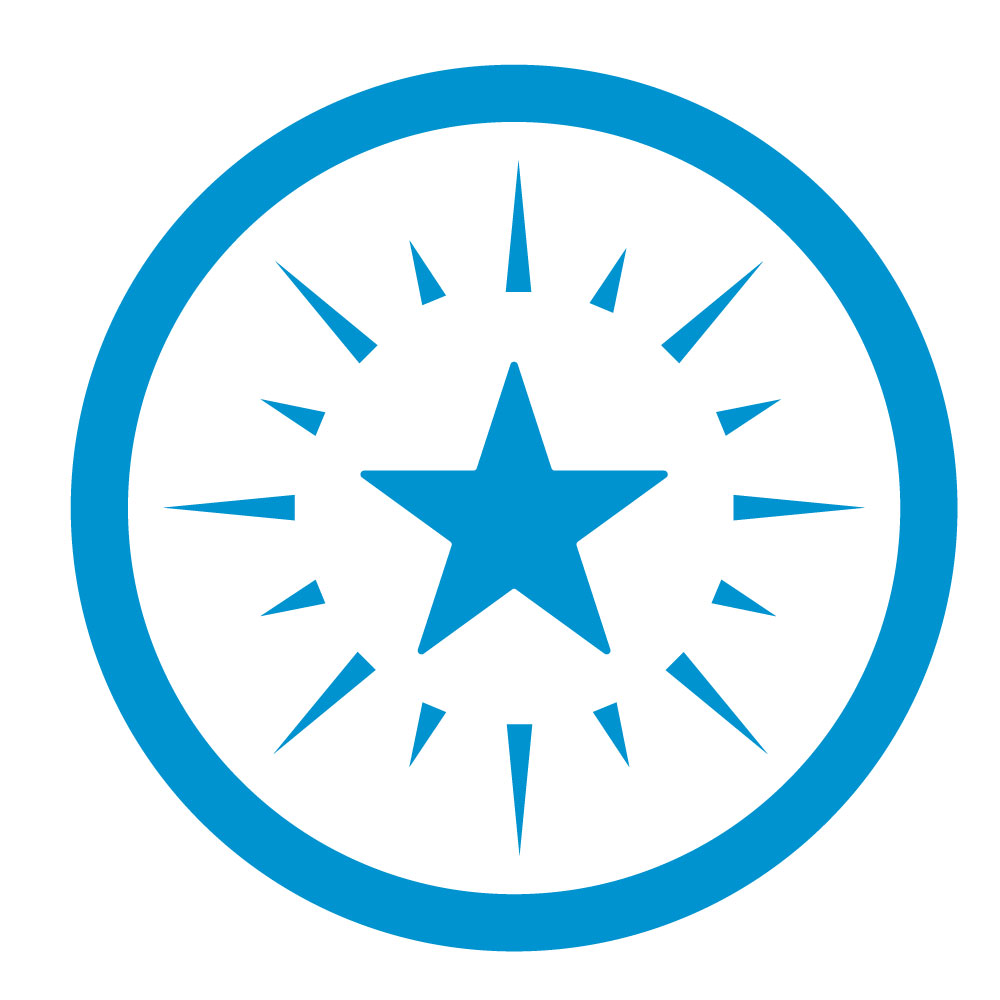
Commitment to Excellence
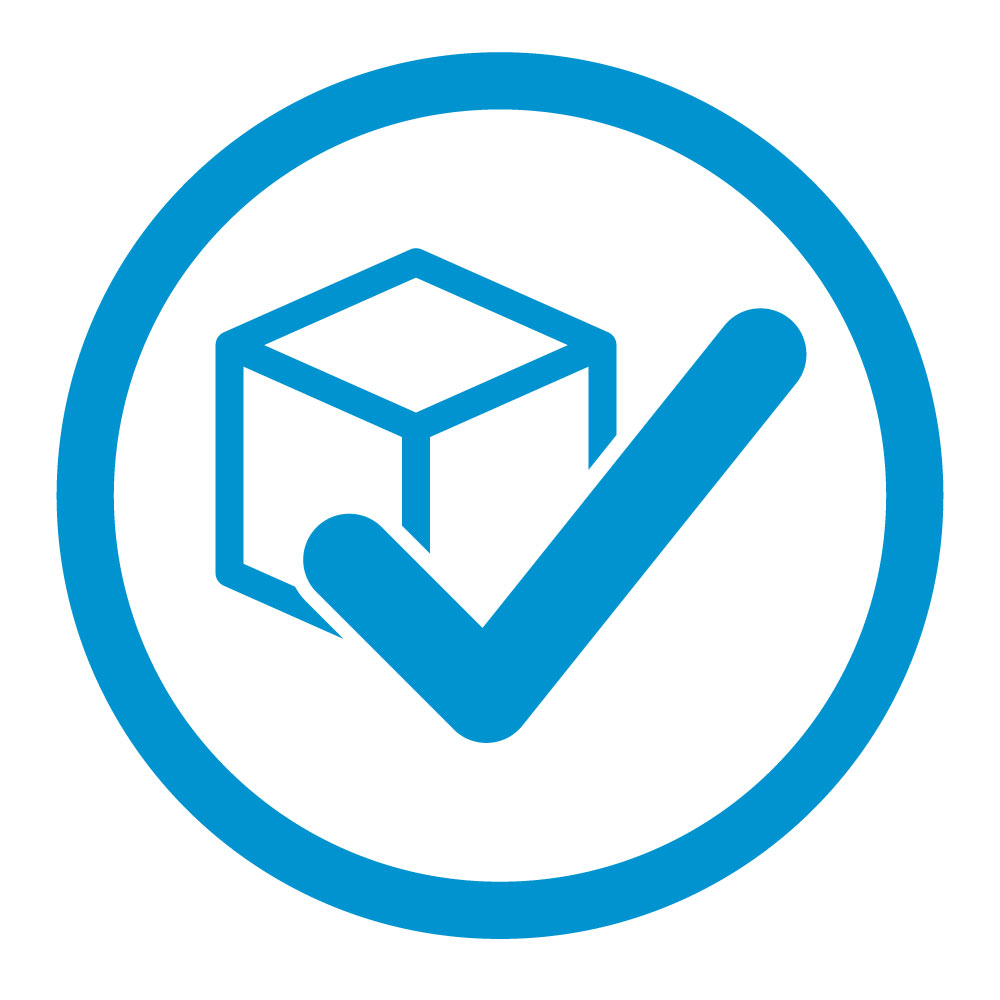
Quality
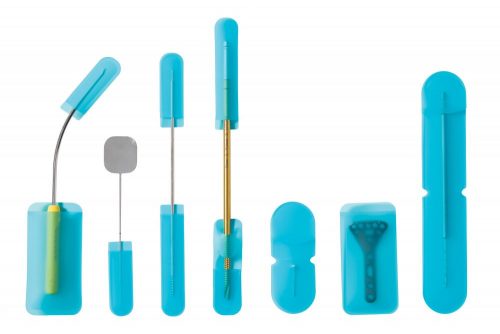
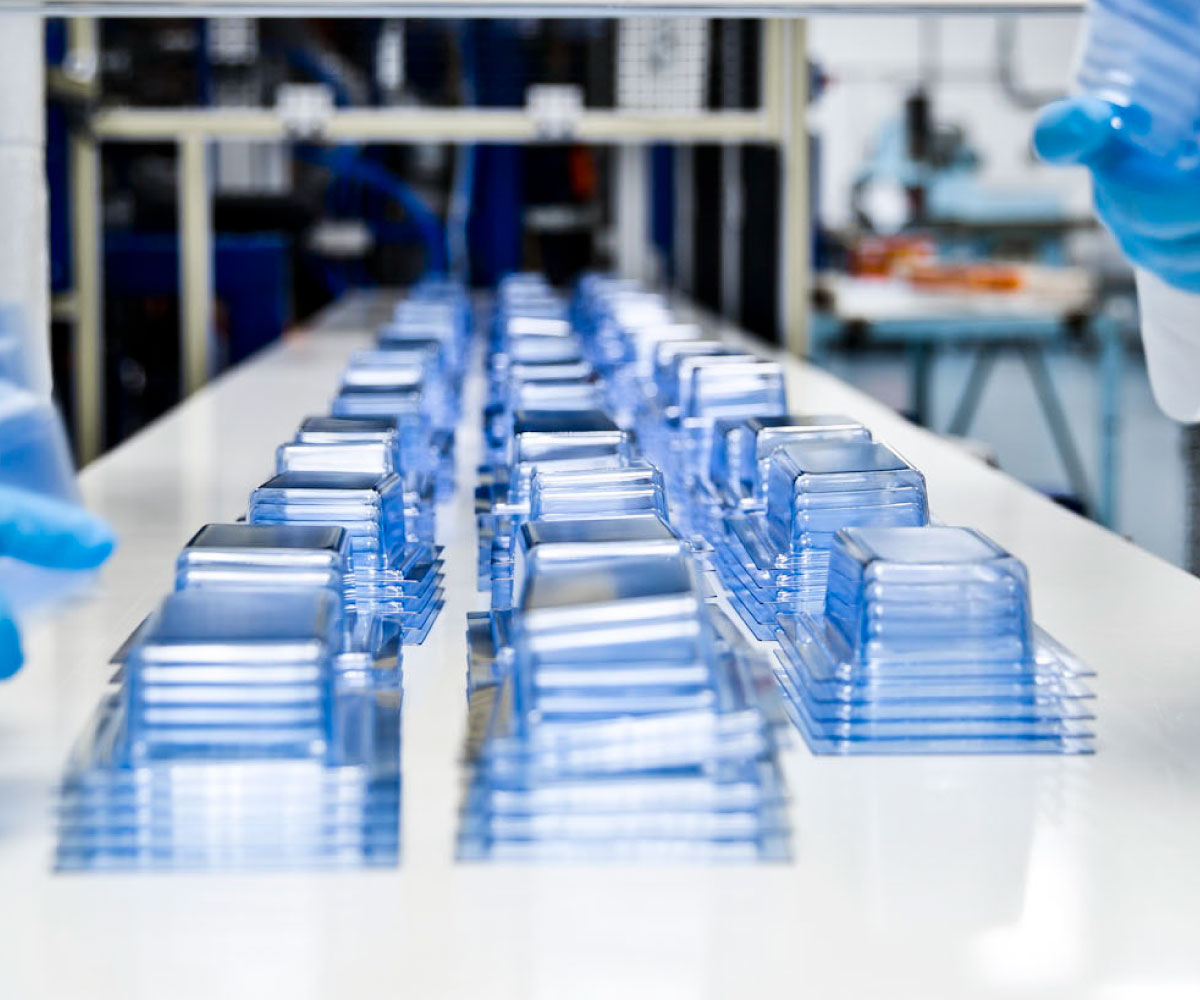
Packaging Expertise
From single barrier trays to double sterile barrier systems, we know how important it is to keep your medical products safe and secure prior to being used in a medical setting or operating room. With our variety of thermoforming platforms, we create the highest quality thermoformed trays, blisters and clamshells to support orthopedic implants, renal-tubing sets, surgical instruments and cardiovascular stents. Beyond just thermoforming, we offer custom inline flexographic printing, die cutting and lift labels that include Tyvek® paper and foil in up to 3 colors. These customized options give you a secure way to seal your product and stabilize fragile devices or preventing abrasion during shipping. We work with you to create not just a package, but a packaging solution.
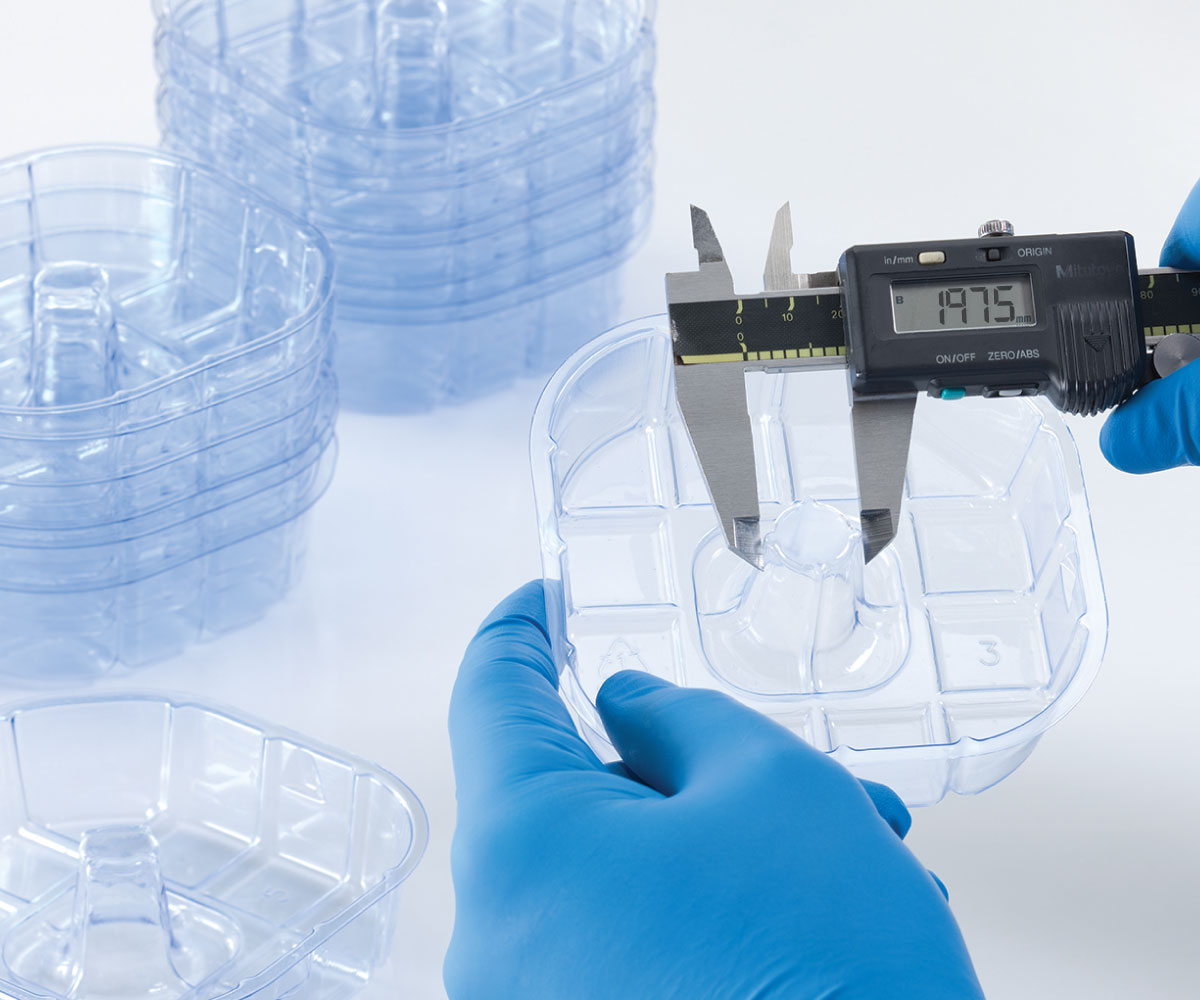
Smart PackagingOur in-house design team has been creating customized medical packaging for over 40 years. Each turnkey medical device and pharmaceutical packaging solution is designed to fit delicate instrument and implants form, fit and functionality. We know how important speed to market is for our medical customer, which is why we staff our sample and prototyping lab 24 hours per day, 7 days per week. Our standard turnaround sample time is 4.5 days, so you get your parts faster to accelerate the review and approval process. Our team works with a variety of materials such as; PETG, HIPS, PP, post-consumer recycled PET and others that can be designed from very small intricate pieces, up to packaging that is 59 inches in length. As medical packaging experts, we know medical packaging can require lower minimums, which is why we are here to support small orders from 500 pieces to orders of 500,000 or more. |
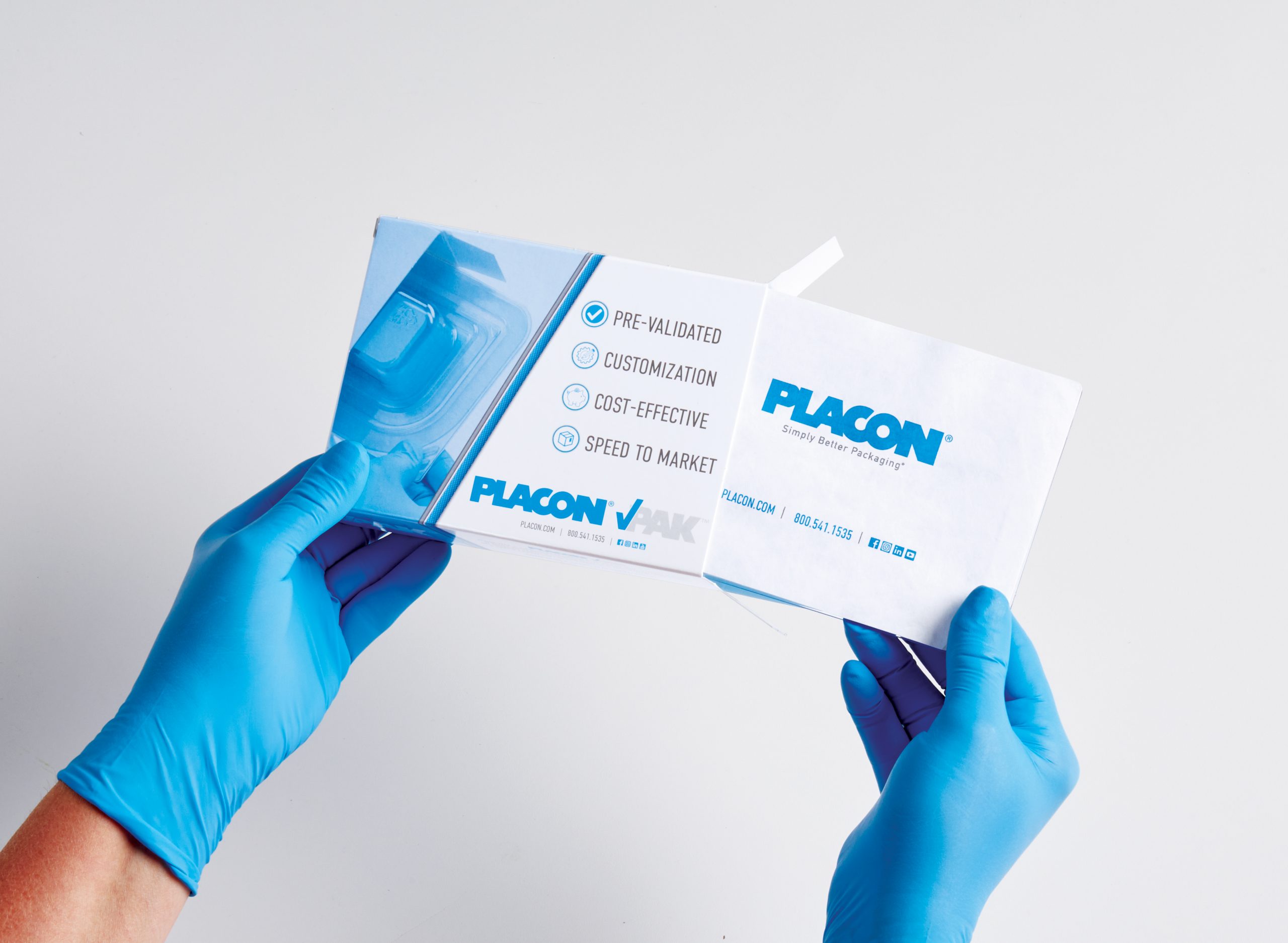
PRE-VALIDATED PACKAGING
For companies that may not have the resources or time to buy the six new tools that this system offers, the Placon VPAK® system gives you the ability to commercialize small new medical device products without a lot of internal resources. Whether you’re a start-up with limited resources or a market leader looking for a more efficient way to bring your product to market, Placon VPAK is the answer.
A smart alternative to foam or vinyl protective packaging is our BargerGard® thermoplastic polyurethane (TPU) packaging. Available as custom-designed parts or stock products, BargerGard protects rough and sharp components including catheters, needles, screws, drills and porous coated implants during shipping or prior to medical usage. This nonabrasive TPU material protects finished, polishes and other delicate surfaces from damage including marring of devices, denting and scratching. BargerGard is die cut and welded into various configurations such as liners, containers, pouches and mounting cards that can be designed specifically for your product. BargerGard is compatible with ethylene oxide (EtO), gamma and eBeam sterilization and is available in material gauges ranging from .005” up to .055”.
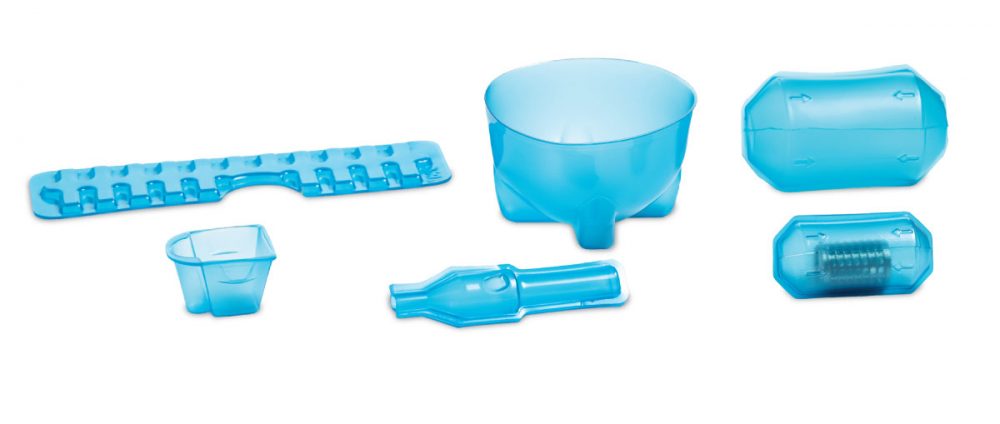
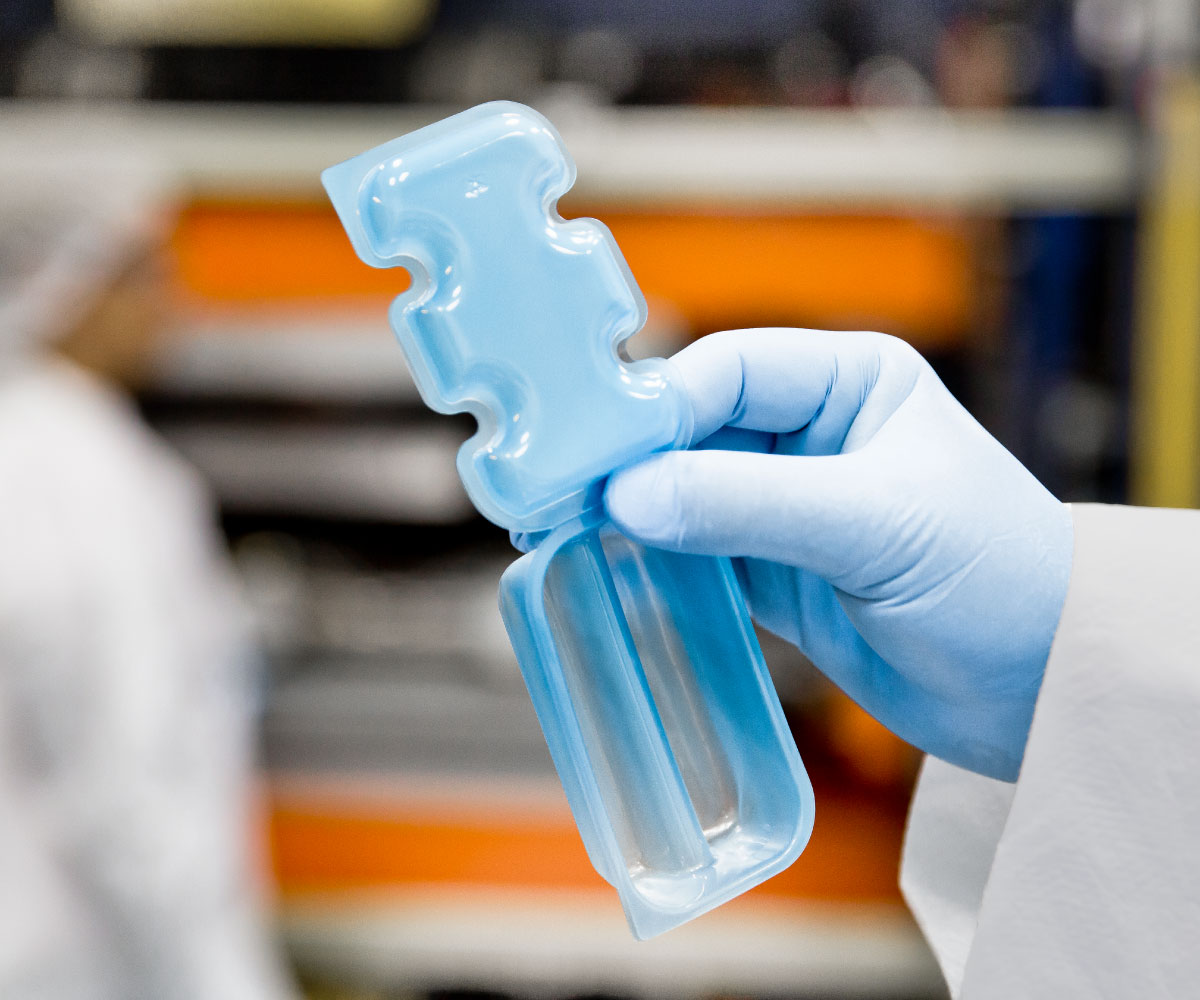
Leader in QualityContinuously raising the bar in plastic packaging solutions, we are committed to integrity and quality in all that we do. Each of our locations have quality department team members on-site to ensure all processes and quality inspections are met per industry inspection guidelines. We have multiple locations and clean rooms to better serve you with ISO 8 clean rooms in each location. We currently hold ISO 9001 and ISO 13485 certifications to better serve our medical customers. Our quality teams implement SPC (Statistical Process Control) procedures and lean manufacturing principles. If you require specific quality standards or guidelines, we work with you to ensure your standards are met specific to your packaging project. It is the responsibility of our customers to determine the fitness for use of our packaging for their products, process, and the end consumer.
|