How Do Materials Recovery Facilities Work?
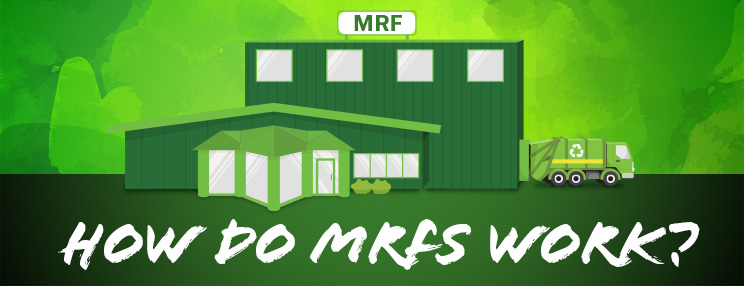
How can MRFs help plastic recovery rates
Recently, more states and cities have been looking to increase recycled content in plastic products to lessen the need for virgin material. To do this, though, there needs to be enough material to fulfill this increased demand. Recovery rates of plastic are very low, only about 28% [1] which includes both single-use materials and those that can be recycled. Something needs to happen to increase recovery and recycling rates so that recycled content demands can be met. Materials recovery facilities (MRF) have played a role in the past in recovery and recycling, and they may be what we are looking for to increase those rates [1].
A material recovery facility is where the different recyclables get separated by their materials so they can be shipped to their respective recycling facilities [2]. Though there are different kinds of facilities, many follow the same process to sort materials. When trucks full of waste enter the facility, it is weighed to keep track of the weight of materials that are entering the facility [2]. The materials are then dumped from the trucks onto a tipping floor, and a large piece of metal gets the materials into a drum feeder which feeds the material onto the conveyer to be sorted [2]. The first sorting process is a manual pre-sorting where workers manually separate the materials and remove those that cannot go through the recycling process [2]. The next part of the process is to remove the paper material from the rest of the contents [2]. To do this, large disks bring the cardboard pieces to the top, then smaller disks bring other pieces of paper materials to the top [2]. As the conveyer keeps moving, metal materials are removed with magnets, and metal materials that can’t be removed via the magnet are removed with an eddy current [2]. Next, the glass is separated from the plastic using a density blower that blows away the low-density plastic materials as the glass continues down the conveyer to be crushed [2]. The plastic then has to be separated by the type of plastic which is done either manually or with optical sorters [2]. As stated previously, there are different types of material recovery facilities. A clean facility is one that only takes in what comes from recycling bins, a dirty facility receives all trash, and a wet facility uses water to separate materials [2].
Though MRFs are effective when it comes to material recovery, there are still some challenges that they face. MRFs don’t usually get materials that are separated as even the clean ones get what comes from our recycling bins, which can contain items that are not recyclable. During the manual sorting process, if a contaminant gets missed and goes through the rest of the process, it can damage the machines within the facility [3]. Items such as plastic straws and plastic shopping bags are just a few examples of items that can’t go through the process but can be easy to miss during manual separation [3]. Through educating people on what can and cannot be recycled, there is a smaller chance of items that cannot be recycled ending up in the recycling stream.
Materials recovery facilities are important to increasing the recycling and recovery rates of plastic to help producers meet recycled content goals. As technologies improve, it would not be surprising to see MRFs make more of an impact toward closing the loop and creating a circular economy!
[1] Accelerating plastic recovery in the United States | McKinsey
[2] What is a Materials Recovery Facility (MRF)? – Scrap Metal Recycling (roanemetals.com)
ABOUT PLACON
For 55 years, Placon has been a leading designer and manufacturer of custom and stock plastic packaging for the food, medical, and retail markets. Placon has manufacturing operations in Madison, WI; Elkhart, IN; Plymouth, MN; and West Springfield, MA, and currently ranked in Plastics News 2020 Thermoformers Ranking Top 20. Placon delivers packaging breakthroughs that inspire better engagement between people and products with industry leading innovation and award-winning packaging designs. For more information, visit www.placon.com.